材料加工設備
レーザー加工機
鋼板を切り出し、必要に応じて曲げ加工や機械加工を実施して、各製造ラインに投入する部品を生産します。
ワークサイズ最大3m×1.5m、出力4.5KWのレーザーヘッドを搭載し、板厚25mmまでの原板を10枚搭載でき、長時間の連続無人運転を行います。
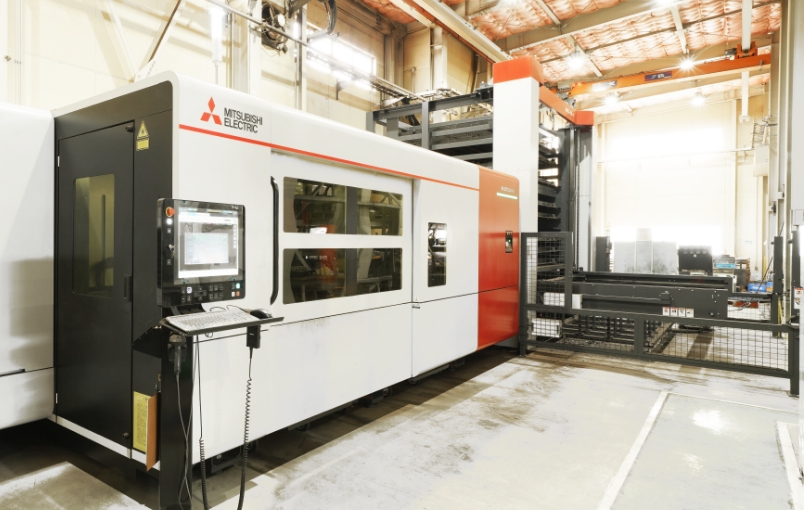
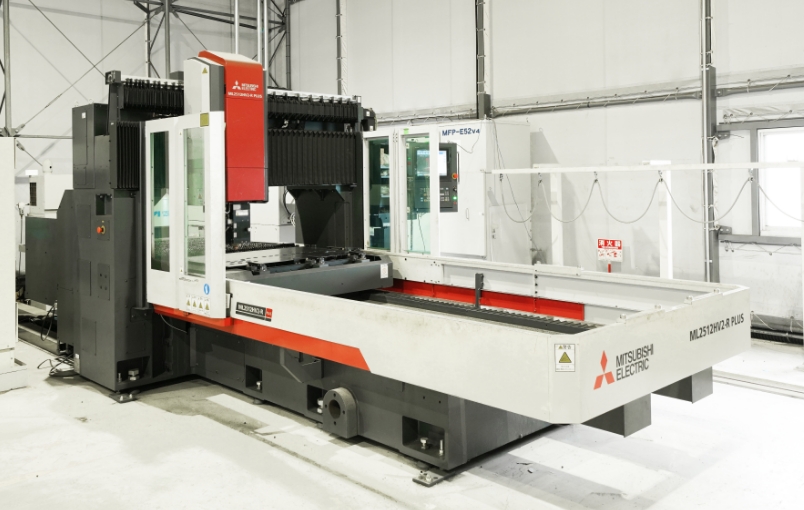
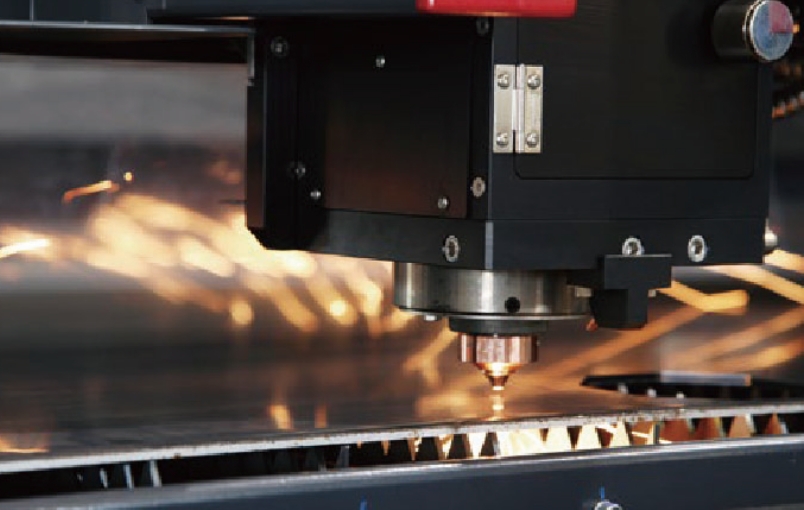
設備詳細
レーザー加工機
設備情報 | 台数 |
---|---|
三菱電機製/ML3015GX-F40 定格出力/4,000W 対象ワーク寸法/3050×1525mm パレットチェンジストッカ数/10段 |
1台 |
プレス・ベンディングマシン
主に機能部品に取り込まれる部品や溶接構造部品に使用されるプレス成形加工を行います。納入する顧客の拠点に合わせた、生産地で製造する事で最適製造・最適供給を実現します。
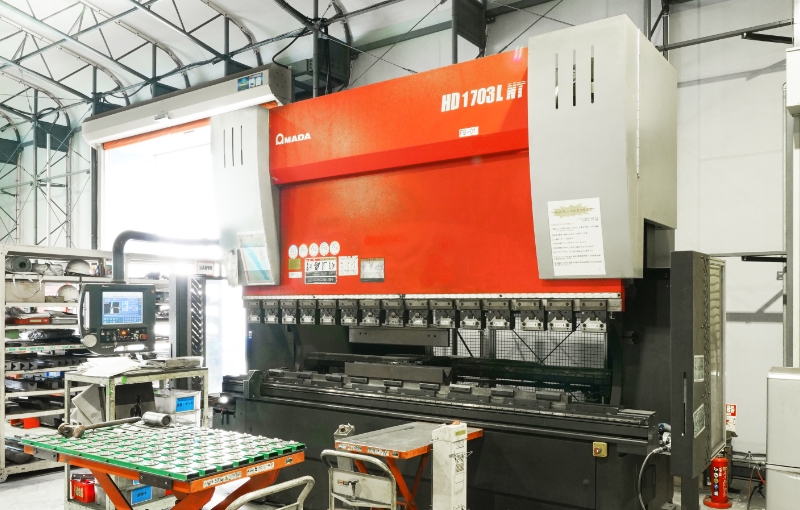
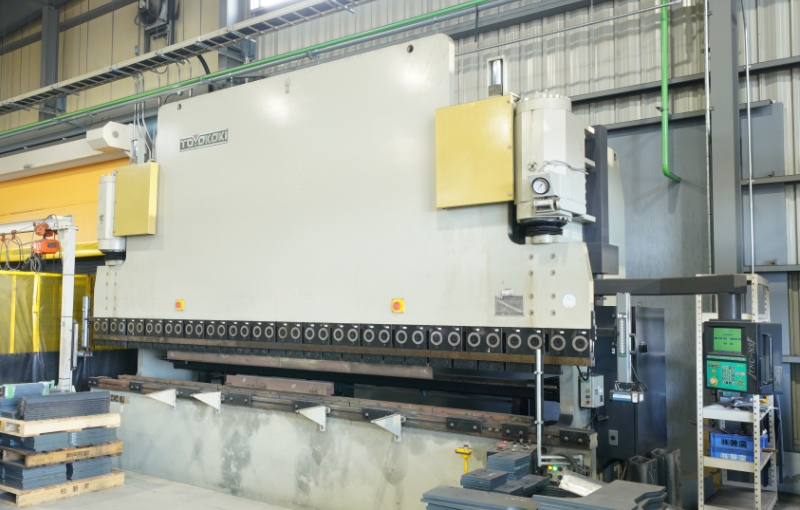
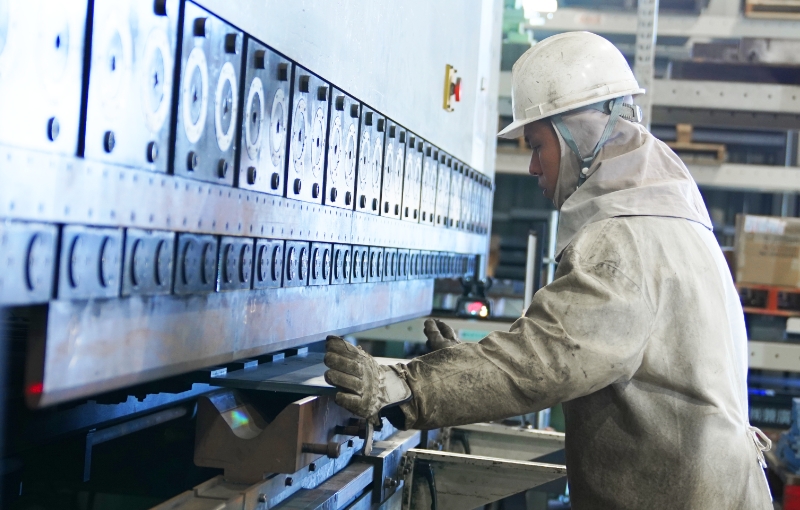
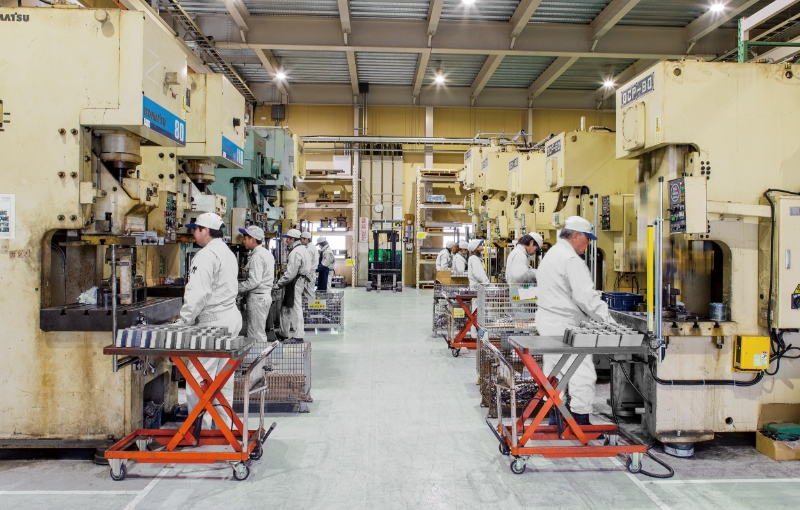
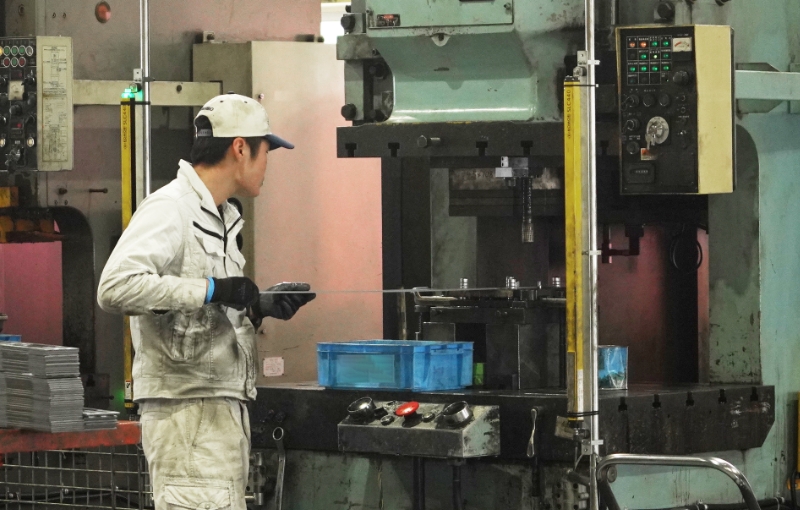
設備詳細
ベンディングマシン
設備情報 | 台数 |
---|---|
アマダ製/HD1703LNT 折り曲げ長さ/3310mm 加圧能力/1700kN 駆動方式/ハイブリッドドライブ |
1台 |
アマダ製/FBD-3512LD 折り曲げ長さ/1200mm 加圧能力/350kN |
1台 |
東洋工機製/HPB-30060AT3 折り曲げ長さ/6000mm 加圧能力/3000kN |
1台 |
機械式プレス機
設備情報 | 台数 |
---|---|
コマツ 150T | 1台 |
コマツ 110T | 1台 |
コマツ 80T | 1台 |
CHZN FONG 80T | 1台 |
CHZN FONG 60T | 1台 |
溶接設備
主に建設機械のキャビンやエンジン・油圧装置類が搭載されるデッキフレームという大物製缶構造物を製造しています。 また、厚物溶接といった多層盛部品も製造し、多品種少量にも対応できる環境と技術を備えています。 その他にも、溶接した部品を塗装し、コーティングも可能としており、一貫生産体制のラインで製造しております。
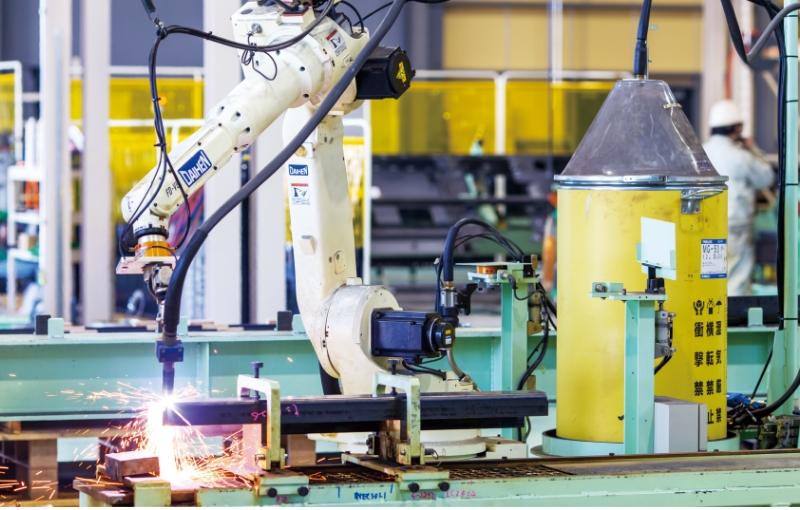
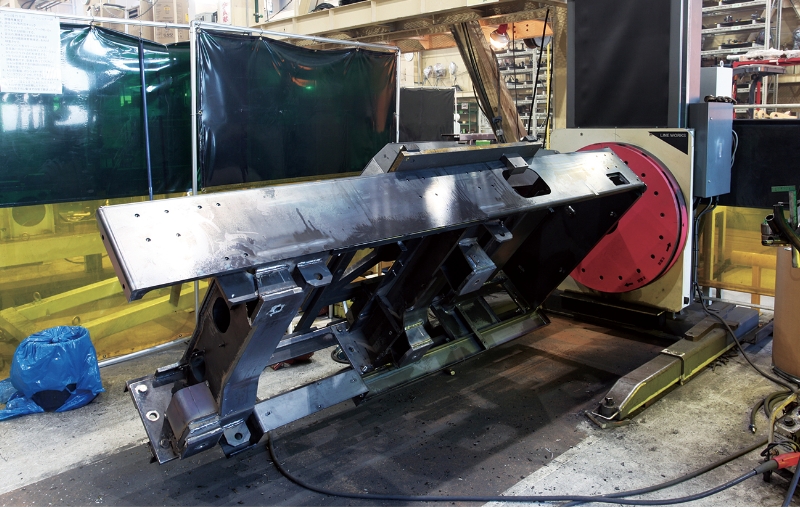
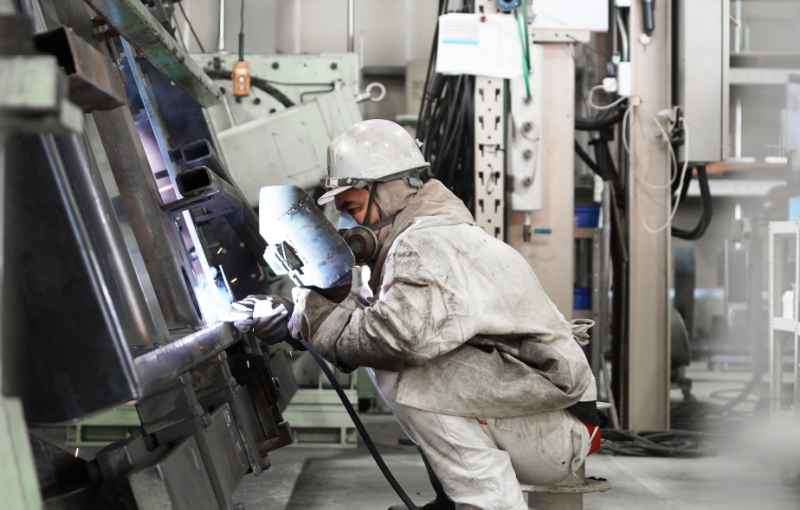
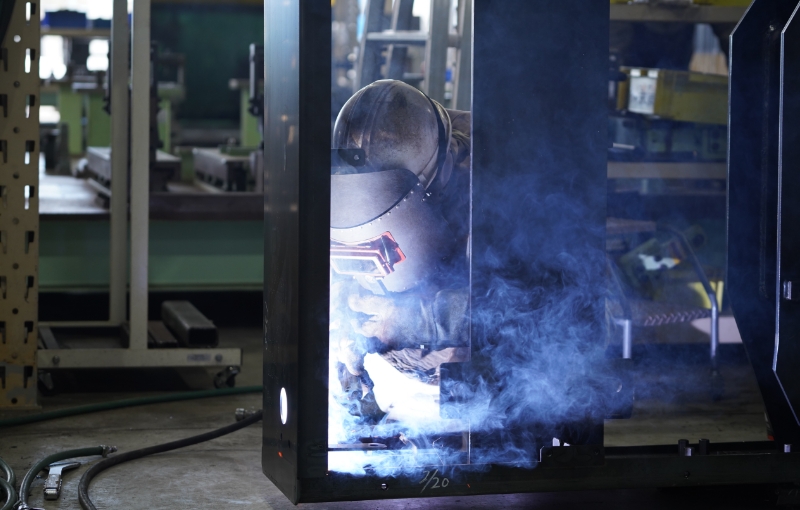
設備詳細
溶接定盤
設備情報 | 台数 |
---|---|
大型特殊定盤/6000mm×1300mm | 1台 |
大型汎用定盤/3050mm×1520mm | 2台 |
半自動溶接機
設備情報 | 台数 |
---|---|
パナソニック製 YD-500KR2 | 3台 |
パナソニック製 YD-350KR2 | 8台 |
パナソニック製 KRⅡ350 | 8台 |
パナソニック製 YD-190SL7 | 2台 |
パナソニック製 YD-160SL7 | 1台 |
ダイヘン製 WB-M350 | 9台 |
ポジショナー
設備情報 | 台数 |
---|---|
ラインワークス製NEW SKETTE 1000CL 形式/片持ち三軸 最大荷重/1000kg | 2台 |
ラインワークス製NEW SKETTE 1000S 形式/二軸 最大荷重/1000kg | 2台 |
溶接・プラズマ切断ロボット
設備情報 | 台数 |
---|---|
ダイヘン製/NB4L2-NJNF 制御軸数/8軸(6軸+2軸ポジショナー) 可搬重量/4kg |
1台 |
ダイヘン製/FD-V6L 制御軸数/8軸(6軸+スライダー+1軸ポジショナー) スライダーストローク/4000mm 可搬重量/6kg |
1台 |
機械加工設備
横中ぐり盤・縦型マシニングセンタ
縦型セルフセンタ
建設機械及び一般産業用等部品の機械加工を行います。特に横中ぐり盤においてはATC60本を設置し、様々な形状の加工を可能としております。
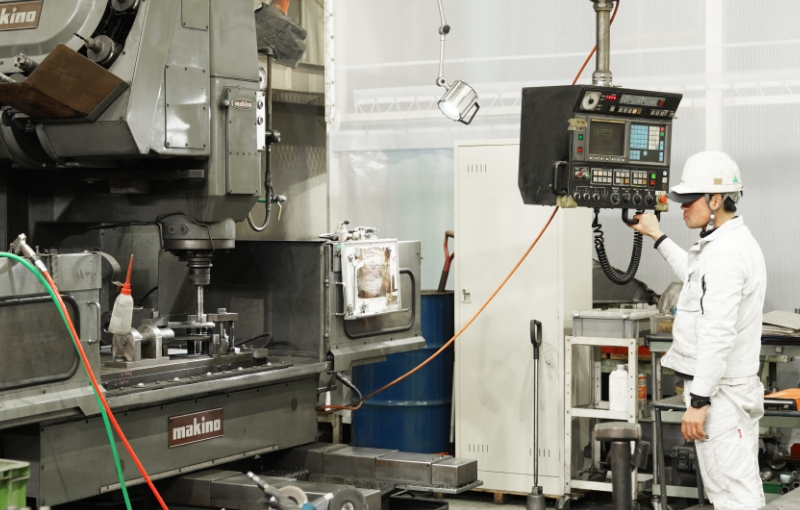
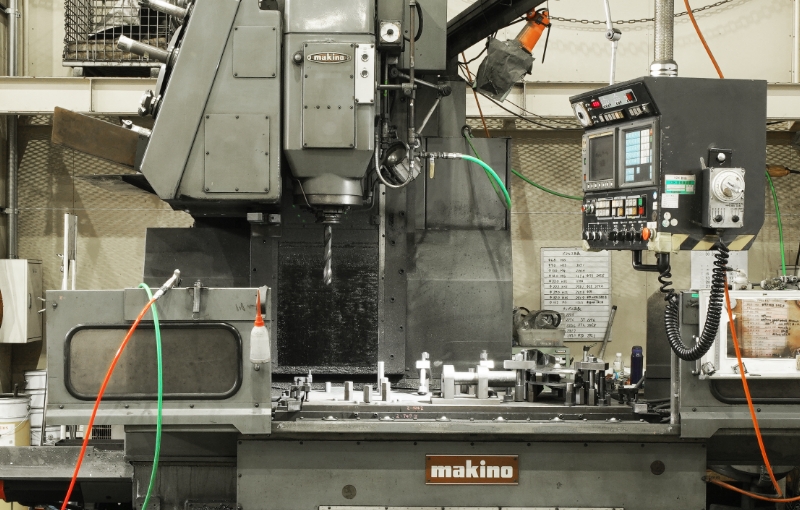
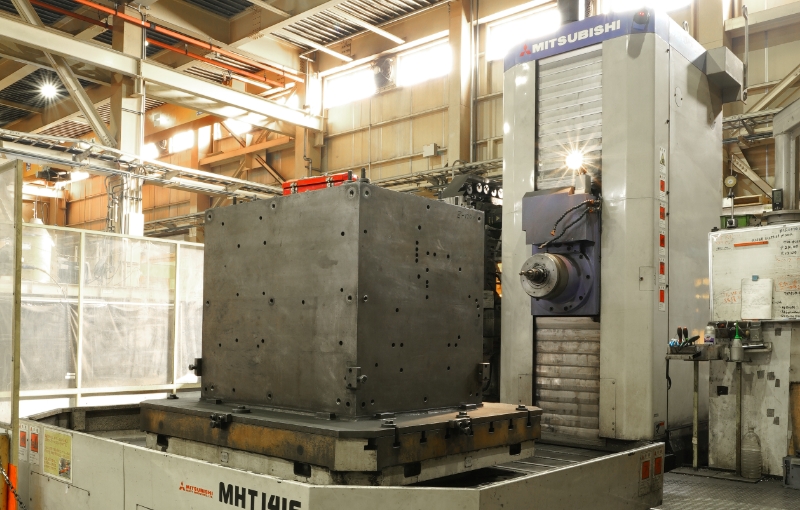
設備詳細
横中ぐり盤
設備情報 | 台数 |
---|---|
三菱重工製MHT1416 主軸直径/130φ テーブル作業面積/1400mm×1600mm 割り出し/0.001° 毎割り出し 積載重量/8000kg 主軸移動量/X軸2000mm Y軸1500mm Z軸1300mm ATC本数/60本 |
1台 |
縦型マシニングセンタ
設備情報 | 台数 |
---|---|
牧野製FNC106-A 主軸直径/128.57φ テーブル作業面積/1400mm×1600mm 積載重量/1500kg 主軸移動量/X軸1050mm Y軸600mm Z軸560mm ATC本数/20本 |
1台 |
CNC複合旋盤・CNC旋盤・NC内面研磨機
ショベルカーのアームやブーム、バケットの可動部に使われる各種の軸受け部品を生産しております。高い加工精度が要求される部品であり、厳しい品質管理体制の元で生産されます。
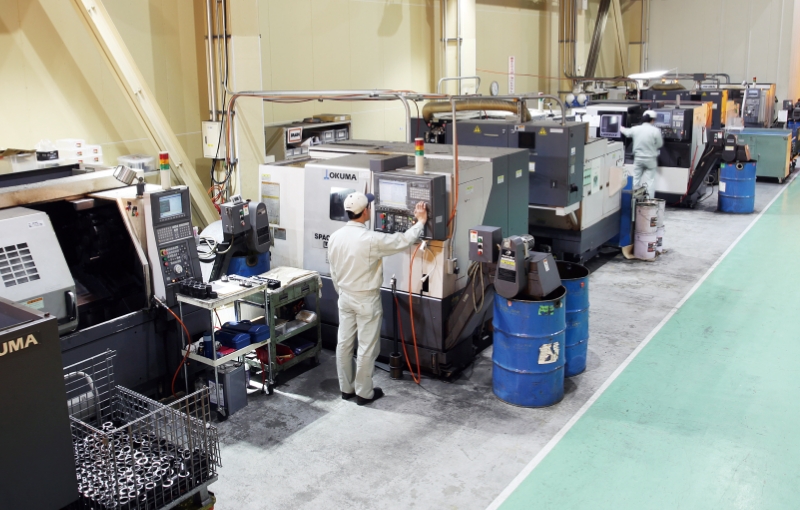
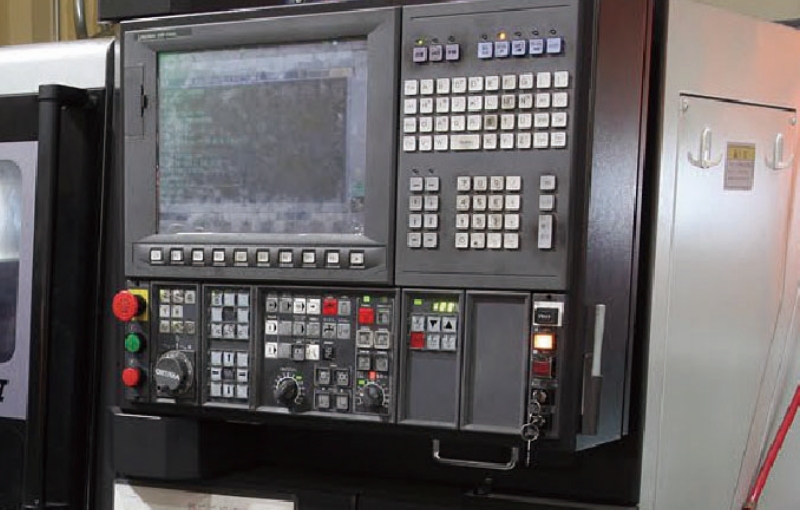
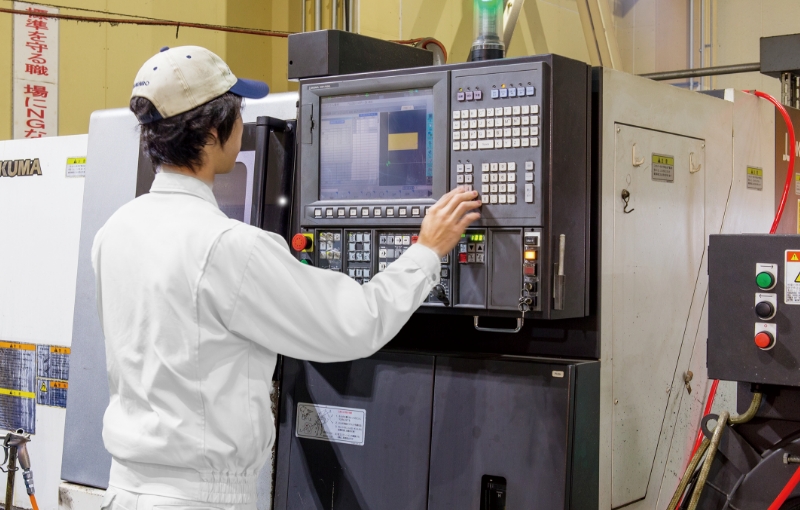
設備詳細
CNC複合旋盤
設備情報 | 台数 |
---|---|
オークマ製LB3000EX-MC500 | 1台 |
オークマ製LB3000EXⅡ-MT | 1台 |
CNC旋盤
設備情報 | 台数 |
---|---|
オークマ製GENOS L400 | 1台 |
オークマ製LCS-25 | 3台 |
オークマ製LCS-15 | 1台 |
北一大隈製LBR370 | 1台 |
NC内面研磨盤
設備情報 | 台数 |
---|---|
オークマ製G1-10N | 3台 |
スロッター
設備情報 | 台数 |
---|---|
山毛鉄工所製MY-150型 | 1台 |
CNC複合旋盤 (無錫長門工場)
設備情報 | 台数 |
---|---|
CNC複合旋盤 | 1台 |
北一大隈製LBR370MM | 1台 |
CNC旋盤 (無錫長門工場)
設備情報 | 台数 |
---|---|
北一大隈製LBR370 | 1台 |
タキザワ製TC203C | 2台 |
NC内面研磨機 (無錫長門工場)
設備情報 | 台数 |
---|---|
北一大隈製LBR370 | 1台 |
オークマ製G1-10N-R | 1台 |
組立設備
ヒンジやドアロックといった、機能部品の組立製造を行なっております。 ドアロック組立装置の開発など、皆で課題検討を行い生産性改善に取り組んでおります。 納入する顧客の拠点に合わせた生産地で製造する事で、最適製造・最適供給を実現します。
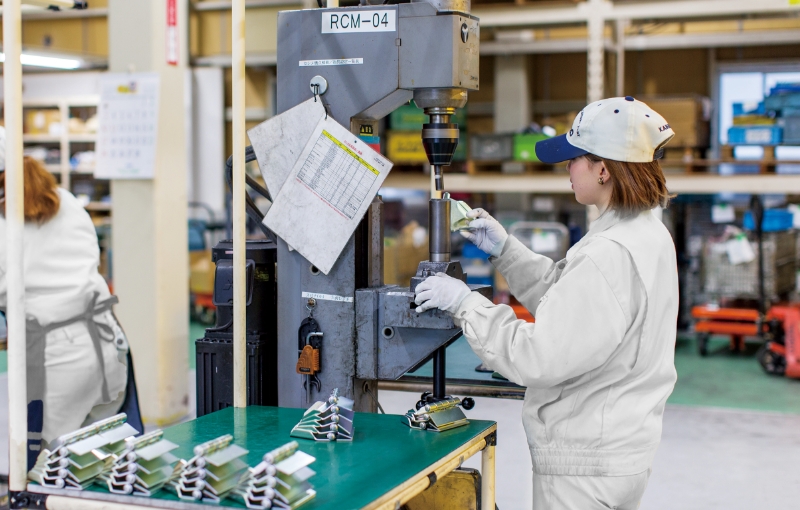
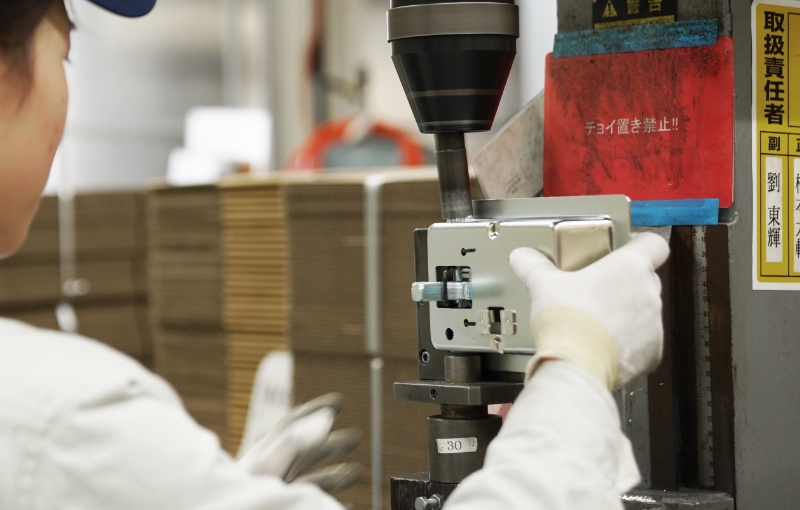
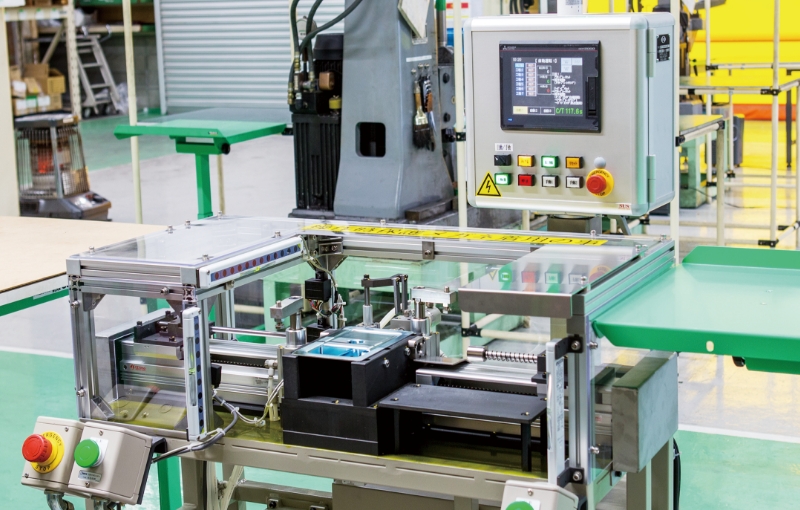
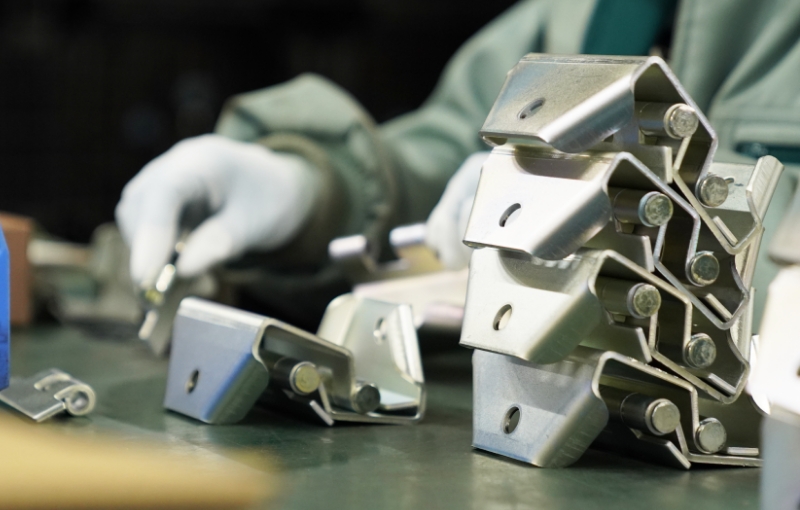
設備詳細
ドアロック組立装置
設備情報 | 台数 |
---|---|
自社開発品 | 1台 |
リベッティングマシン
設備情報 | 台数 |
---|---|
吉川鐵工製 US-150 | 2台 |
吉川鐵工製 US-70 | 3台 |
スポット溶接機
設備情報 | 台数 |
---|---|
パナソニック製 YR-350CM2 | 2台 |
リベッティングマシン(上海工場)
設備情報 | 台数 |
---|---|
吉川鐵工製 US-150 | 5台 |
吉川鐵工製 US-70 | 3台 |
塗装設備
自社で製造された大型構造部品の塗装を行っています。塗装前のショットブラスト加工から本塗装、乾燥まで、当社保有の塗装ラインにて対応が可能です。
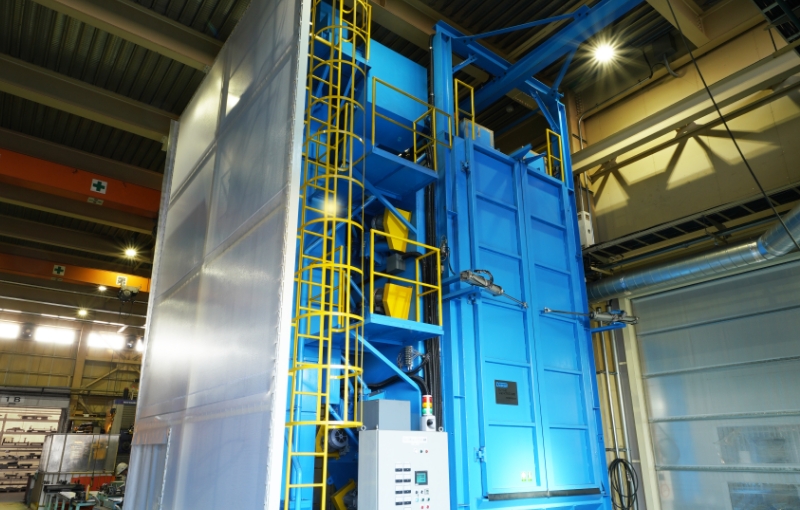
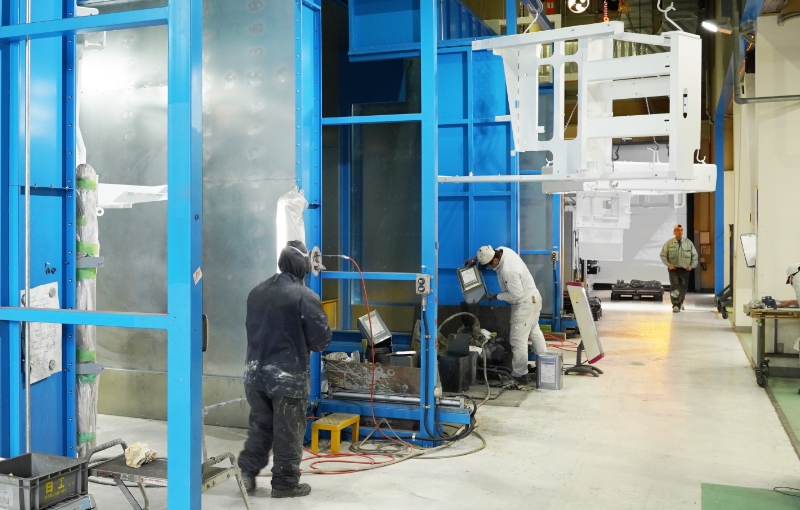
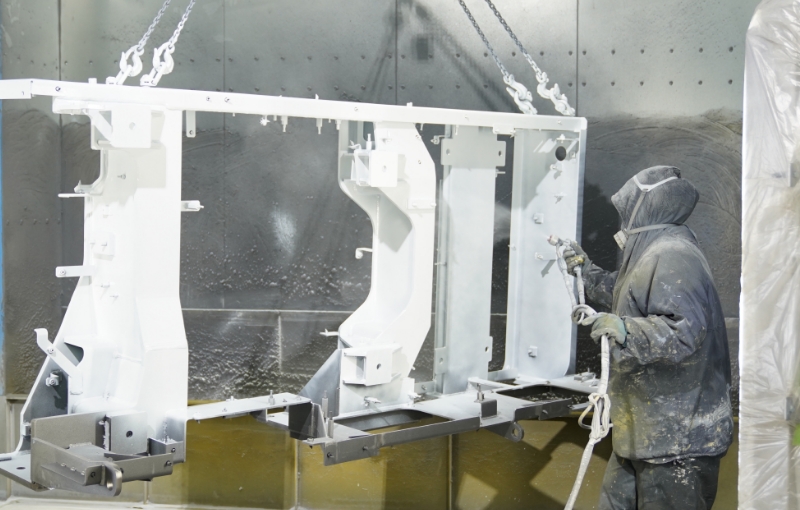

設備詳細
ショットブラスト
設備情報 | 台数 |
---|---|
大研機械株式会社 処理能力:最大高さ 3600㎜ 有効研掃直径 Φ1650㎜ 最大重量 1000㎏ 研掃材 スチールショット(Φ0.8㎜) |
1台 |
塗装ブース
設備情報 | 台数 |
---|---|
空気設備工業株式会社 処理能力:有効寸法(W1650×L2710×H1650) 最大重量 1000㎏ |
2台 |
乾燥炉
設備情報 | 台数 |
---|---|
空気設備工業株式会社 処理能力:有効寸法(w2200×L3900×H4050) 炉内雰囲気温度 80℃ 熱風発生器:関西電熱(ヒーター 45kw) 最大重量 1000㎏ |
1台 |
塗装機器
設備情報 | 台数 |
---|---|
WAGNER スプレーガン GA4700AC エアーコートガン 供給ポンプ コブラ40-25 高圧ダイアフラムポンプ |
1台 |
製造支援設備
検査機器
大物製缶現場では高精度な測定を可能とするポータブル三次元測定機に加え、広範囲でも1人でも誤差なく測定できるワイドエリア対応三次元測定機を利用することで、正確な数値を少人数に効率よく測定しています。 また、構造が複雑な小型の部品は、全自動CAD変換機能が搭載された3Dスキャナ型の三次元測定機を利用し、作業効率と品質を両立しています。
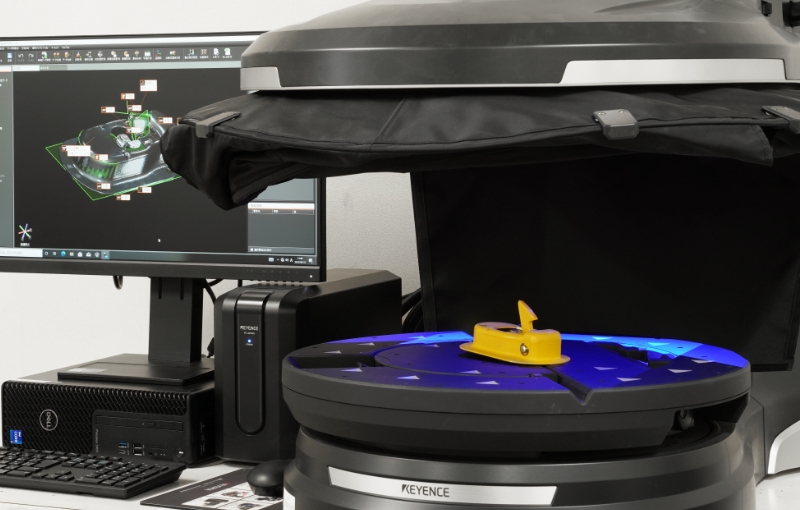

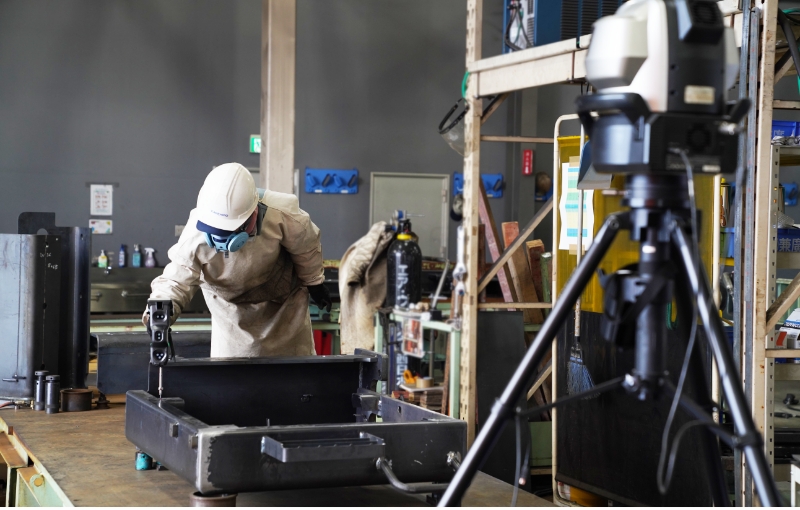
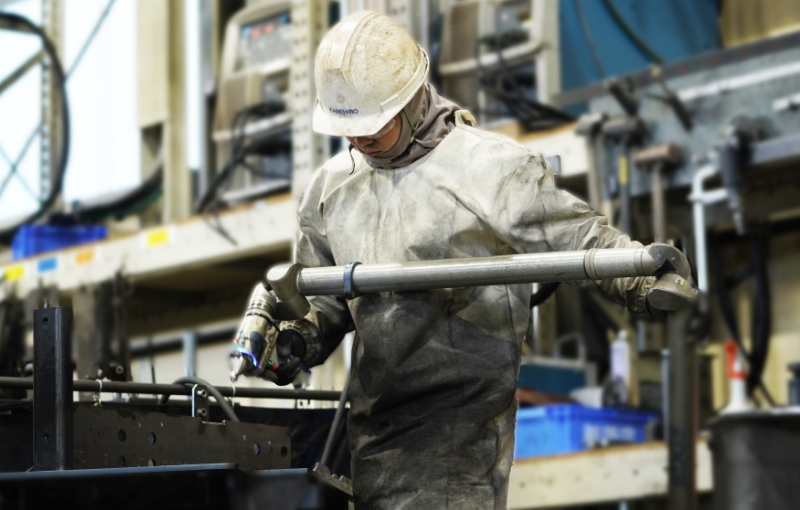
設備詳細
3次元測定機
設備情報 | 台数 |
---|---|
ポータブル三次元測定機
FARO製 FARO-ARM EDGE 測定範囲 3.7m |
1台 |
ポータブル三次元測定機
FARO製 PRIME 測定範囲 3.7m |
1台 |
キーエンス製 三次元測定機 3Dスキャナ型 VLシリーズ |
1台 |
キーエンス製 ワイドエリア三次元測定機 WM-3500 |
1台 |
形状測定器
設備情報 | 台数 |
---|---|
東京精密製 CONTOURECORD160G | 1台 |
投影機
設備情報 | 台数 |
---|---|
ミツトヨ製 PJ-H30 | 1台 |
面粗度計
設備情報 | 台数 |
---|---|
ミツトヨ製 SJ-400 | 1台 |
形状測定器(上海工場)
設備情報 | 台数 |
---|---|
東京精密製 CONTOURECORD160G | 1台 |
面粗度計(上海工場)
設備情報 | 台数 |
---|---|
ミツトヨ製 SJ-400 | 1台 |
3D CAD
業務を支援するシステムとして3DCADによる3D設計及び応力解析等を行なう数値シミュレーションシステムを導入しています。また開発室では製品の破壊試験や耐久性試験を行なう設備を有しています。これらを駆使し、小物機構部品の自主開発を行い、オリジナルな機構を持つ機構部品をお客様に提案する活動を行っております。これらの活動を通じてお客様の設計ニーズに開発初期から取り組ませて頂く事で、お客様のニーズに的確にお応えするフロントローディング活動を展開致します。
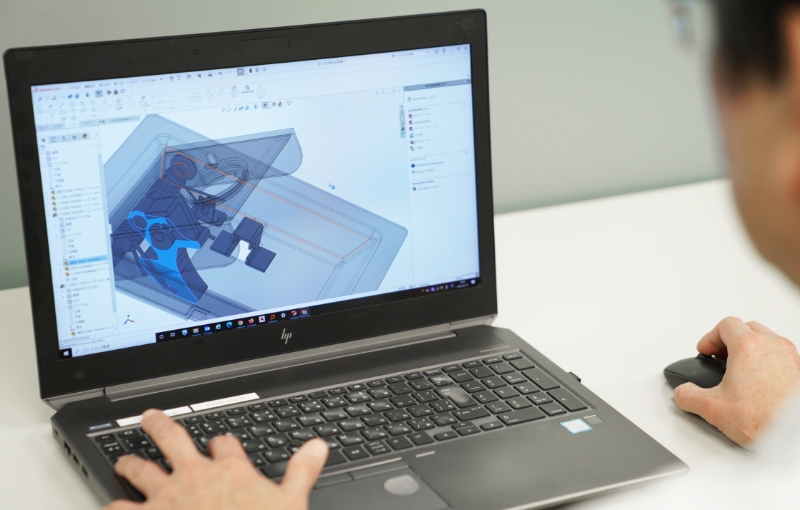
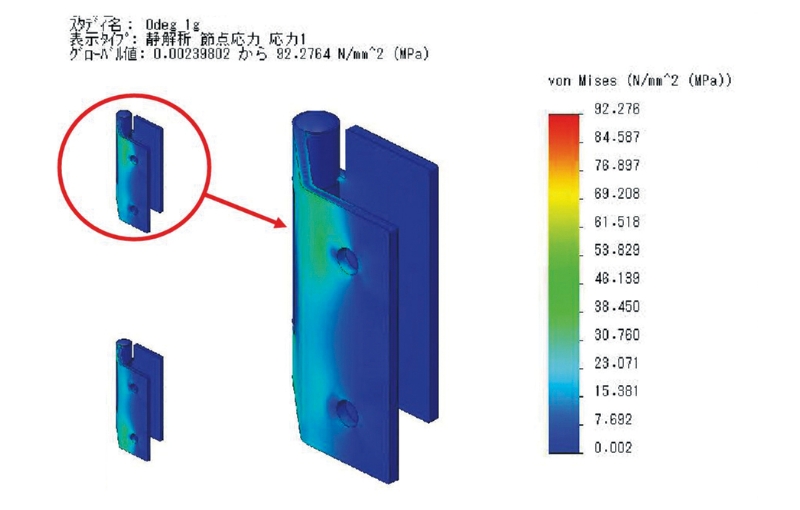
設備詳細
3DCAD
設備情報 | 台数 |
---|---|
DASSAULT SYSTEMS社製 SolidWorks Professional | ライセンス数1台 |